







Process map: Everything you need to know
What is a process map?
It is a visual representation of all key processes within a company or organization. It provides an overview of how different processes and departments are connected and shows the relationships and interfaces between the processes. Visualizing the process map makes it clear which dependencies exist, where weak points lie, and where opportunities for process optimization arise.
Compared to detailed process descriptions, the process map presents processes at a higher level and offers a macro view of the company. It does not show every individual step of a process, but rather the main processes and their interrelationships.
Important elements of a process map:
- Main processes: These are the focus of the map and represent the company's core activities, such as production, customer service, or research.
- Supporting processes: These include processes that support the main processes, such as IT, human resources, or purchasing.
- Management processes: These are processes that ensure the company's objectives are achieved, such as strategic planning or quality management.
The process map is often used within a quality management system and is particularly useful in industries where high standards must be maintained, such as ISO 9001 certification. It not only provides an overview of company processes but also helps identify risks and ensure compliance with standards.
The advantages of a process map
A well-designed process map offers numerous benefits for companies and organizations:
- Clarity and transparency: It provides a clear overview of all processes within the company. It shows how the various processes are linked and where there is potential for optimization.
- Process optimization: By identifying interfaces and dependencies, inefficient or duplicate processes can be quickly uncovered and optimized.
- Improved communication: A process map facilitates internal communication by providing all employees and departments with a common basis for understanding processes.
- Quality management: Process maps are particularly valuable in the context of ISO 9001 certification, as they help ensure compliance with quality standards and promote continuous improvement.
- Employee training: New employees can be integrated into the company's structures more quickly thanks to the visual representation of processes.
Process map examples from various industries
Process maps are used in almost every sector, from industry to public institutions. Here are some examples:
1. Process map in the hospital
In a hospital, processes are often very complex, as different departments such as the emergency room, surgery, nursing, and administration work closely together. A process map for a hospital could depict the following main processes:
- Patient admission: From the patient's arrival to assignment to a department.
- Treatment and care: All medical and nursing measures.
- Discharge management: Processes for discharging patients, including follow-up care planning.
- Administrative processes: Such as managing patient records or billing.
2. Process map at universities
At universities, teaching, research, and administration are the central processes. A process map for a university could include the following main processes:
- Curriculum planning: Organization of courses and seminars.
- Research: From project planning to implementation and publication of results.
- Student administration: Enrollment, examination administration, and graduation management.
- Supporting processes: IT support, library services, and administrative tasks.
Process map and ISO 9001
Within the framework of the ISO 9001 standard, the creation of a process map is an important prerequisite for documenting a company's processes and ensuring continuous improvement. An ISO 9001 process map provides a structured overview of core processes, management processes, and supporting processes. It shows how these processes are interrelated and supports compliance with quality standards. Companies that are certified according to ISO 9001 can ensure that all standard requirements are met by creating a process map.
How do you create a process map?
Creating it requires a structured approach. Here are the steps you should follow:
1. Define goals:
Before you begin creating a process map, determine what your goals are for the process map. Do you want to improve efficiency, identify weaknesses, or support your ISO certification?
2. Identify processes:
List all main processes, supporting processes, and management processes. This includes all essential processes within the company, such as production, logistics, purchasing, quality management, and customer service.
3. Assign process owners:
Determine which departments or individuals are responsible for each process. This makes it easier to assign tasks and responsibilities.
4. Visualize processes:
Create a graphical representation of the processes that shows the interactions between the different processes. Use standardized symbols to create clarity and ensure the process map is easy to understand.
5. Review and optimize the process map:
Review the created map together with the relevant departments and make improvements as needed. A process map should be updated regularly to reflect new developments and changes.
How Dialogbild can help you create a process map
Creating a clear and concise process map requires expertise and experience in visualizing complex processes. Dialogbild, as an experienced agency, can be your ideal partner. We offer customized solutions that enable you to visualize your processes clearly and effectively.
1. Customized Process Visualization
Dialogbild creates customized process maps tailored to the needs of your company. We ensure that all processes are clearly presented and process responsibilities are clearly identifiable.
2. Process Optimization through Visualization
Our visualizations not only help you to depict processes, but also to identify optimization potential. By clearly visualizing interfaces and dependencies, weak points can be uncovered and processes can be designed more efficiently.
3. Process Maps for Specific Industries
Whether you're a hospital, university, or industrial company – we have experience in various industries and create process maps that meet the specific requirements of your industry.
If you need help creating your process map, DIALOGBILD is your reliable partner. Contact us today to learn more about our customized visualization solutions.
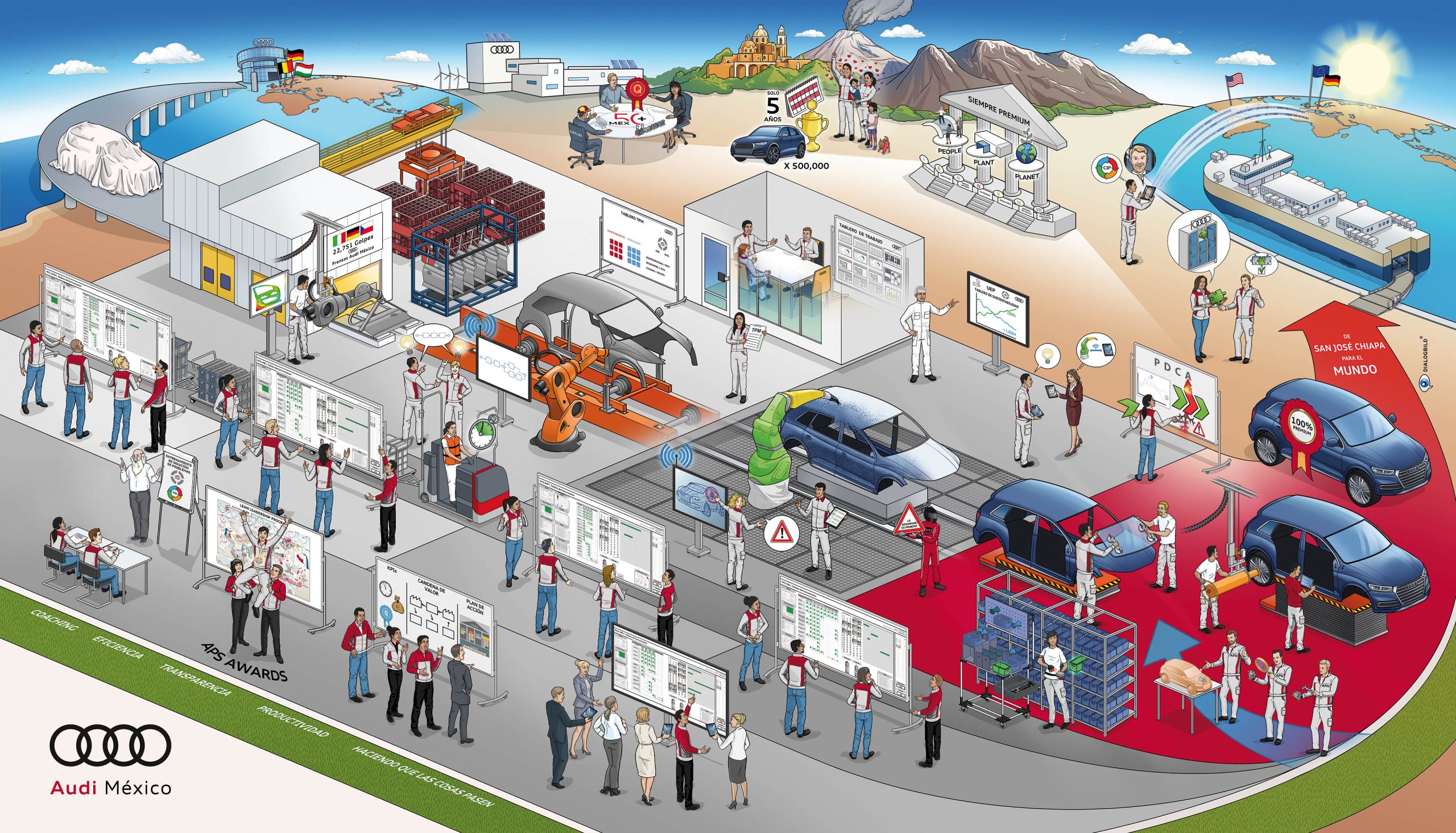
THE AUDI PRODUCTION SYSTEM
AUDI AG has one of the most flexible and efficient production systems in the automotive industry: The Audi Production System (APS) is based on the basic principles of stroke, flow, pull and perfection. Audi consistently implements these principles in production and throughout the company. The APS can only work successfully with good cooperation between all business areas along the process chain. As a result, Audi achieves short cycle times, low inventories and high productivity in production with an annual rate of increase of up to ten percent. This Audi production system now has to be implemented in the plant in Mexico in the coming years. ...
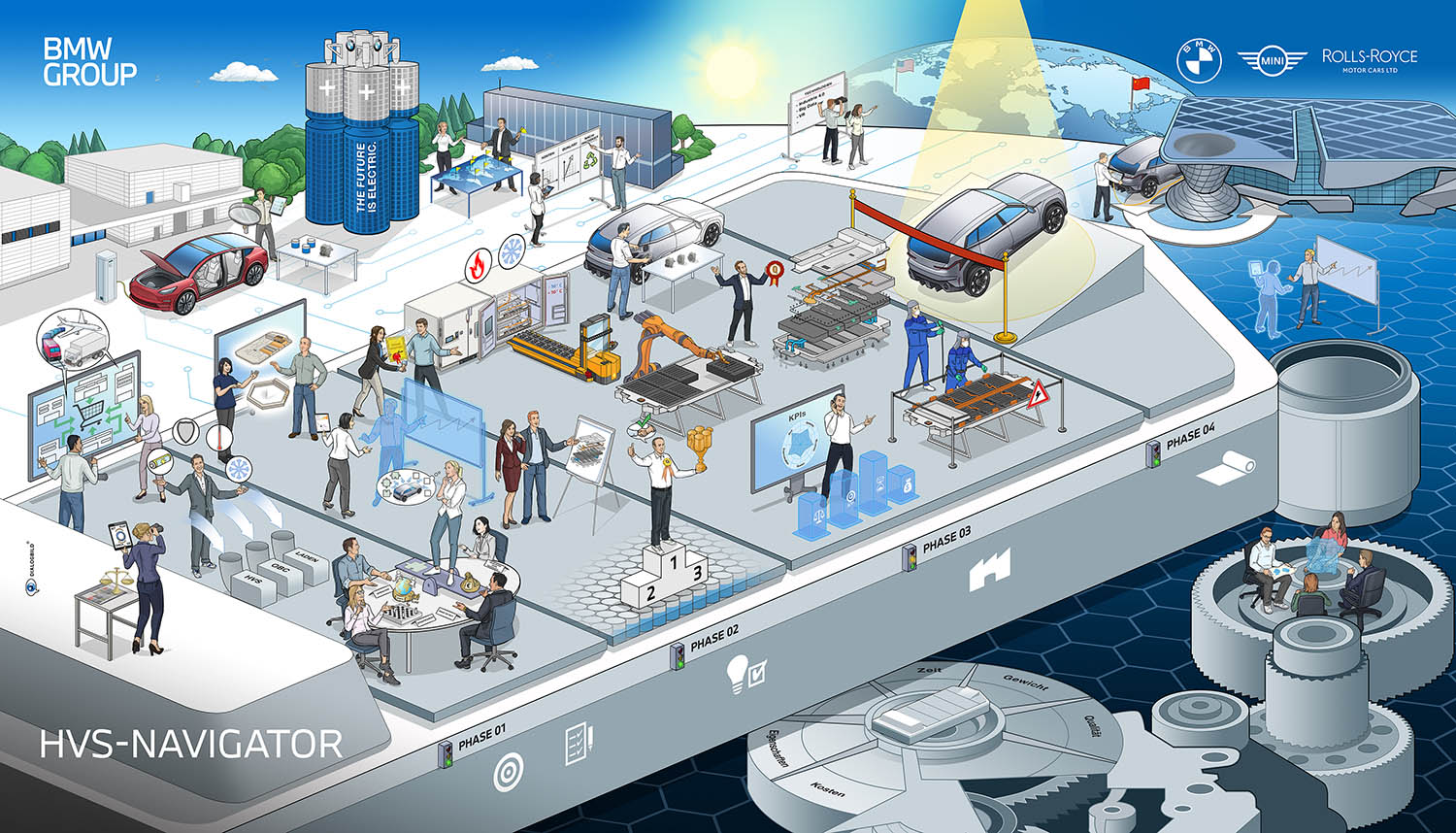
E-DRIVE DEVELOPMENT
THINKING ABOUT TOMORROW'S OPPORTUNITIES
With 31 production and assembly plants in 15 countries, the BMW Group is today one of the world's leading premium car manufacturers. The BMW Group is responding to the current age of electric mobility with clear and forward-looking visions of electric cars that are already thinking about the possibilities of tomorrow. The processes along the way are complex and require coordinated and targeted development steps. ...
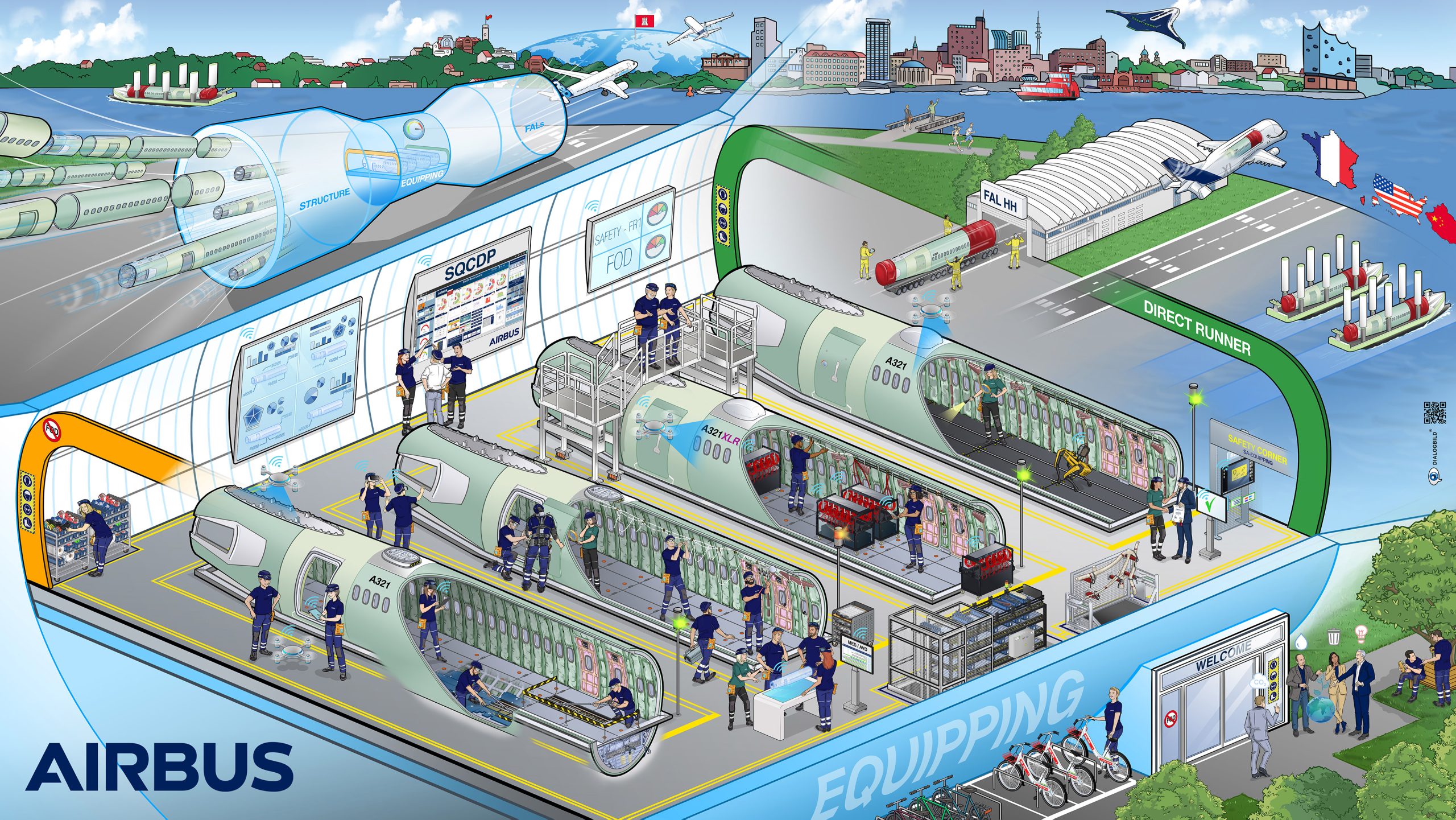
SINGLE AISLE
EQUIPMENT ASSEMBLY 2.0
Aircraft of the A320-family from Airbus are among the best selling aircraft worldwide. The depicted A321 model is a single aisle airplane with a capacity of up to 240 passengers and a range of up to 5,500 kilometers. As XLR-variant the airplane, equipped with additional tanks, is meant to reach a range of up to 8,700 kilometers. As final member within the Airbus Aerostructures GmbH in the location Hamburg-Finkenwerder, our picture depicts the entire system installation in the rear part of the assembly section and the further handover to Airbus FALs (Final Assembly Lines) in Germany, France, China and the USA. ...
Frequently asked questions
What is a process map?
A process map is a visual representation of the key processes within a company or organization. It shows the relationships between different processes and departments and provides an overview of the main processes, supporting processes, and management processes. The process map is used to optimize processes and improve communication within the company.
Why is a process map important?
A process map helps bring transparency to company processes. It facilitates the identification of weak points and optimization potential. It also serves as a basis for quality management, especially for ISO 9001 certifications. Process maps promote collaboration between departments and improve internal communication.
What are the benefits of a process map?
- Transparency: All processes are clearly presented, making dependencies and interfaces clear.
- Process optimization: Inefficient or redundant processes can be identified and optimized more quickly.
- Improved communication: The visual representation facilitates understanding of processes and promotes collaboration.
- Quality management: Process maps are a valuable basis for certifications such as ISO 9001.
- Employee training: New employees can be trained more quickly thanks to the visual representation of processes.
What are some examples of process maps in different industries?
- Hospitals: Shows processes from patient admission to discharge, including treatment and administrative processes.
- Universities: Shows processes such as curriculum planning, research, and student administration.
- Industry: Visualizes manufacturing processes, quality management, and logistics.
How do you create a process map?
- Set goals: Clarify what you want to achieve with the process map (e.g., optimization or ISO certification).
- Identify processes: Record all main, supporting, and management processes in the company.
- Assign process owners: Define responsibilities for each process.
- Visualize processes: Use graphical representations to clearly depict the processes.
- Review the process map: Optimize the representation and have it updated regularly.
What is an ISO 9001 process map?
An ISO 9001 process map shows the core company processes related to the quality management system. It helps meet the standard requirements by clearly documenting all relevant processes and their connections. Such a map is important for ISO certification because it forms the basis for continuous process improvement.
What role does a process map play in a hospital?
In a hospital, a process map is an essential tool for coordinating complex processes between medical and administrative departments. It shows the flow from patient admission through treatment to discharge and ensures that all interfaces function smoothly.
What are the benefits of a process map at universities?
A process map at universities provides a structured overview of central processes such as curriculum planning, research, and student administration. It helps optimize processes by visualizing the links between different departments and administrative processes. This facilitates increased efficiency and ensures better coordination of academic and administrative activities.
How can Dialogbild help with the creation of a process map?
In addition to strategy pictures or dialog pictures for leadership principles, Dialogbild offers customized visualization solutions for creating process maps. We support companies in presenting their processes clearly, understandably, and efficiently. Our services include:
- Customized process visualization: Creation of maps tailored to your specific needs.
- Process optimization: Identification of weak points and potential for improvement.
- ISO 9001 support: Assistance with the creation of a process map for ISO certification.
- Industry-specific solutions: Process maps for hospitals, universities, and other industries.
How often should a process map be updated?
A process map should be reviewed and updated regularly, especially when processes change or are optimized. An annual update is recommended to ensure the map remains relevant and useful.